We may have just seen the start of a quantum shift in house construction in New Zealand this week. With the opening in Auckland of a new house building factory by Fletcher Building, named Clever Core, Aotearoa may have at last taken a major move towards prefabrication of housing and therefore the start of a whole new way of doing things.
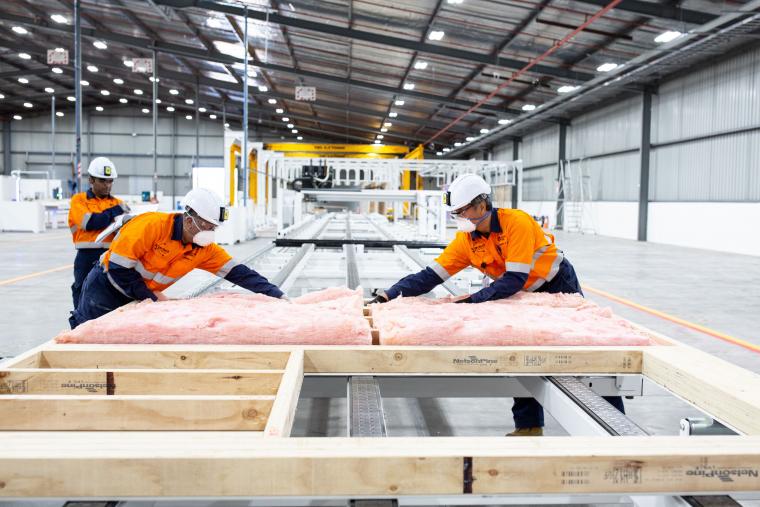
Some questions:
Will this speed up construction time? Undoubtedly, Yes, both on-site and off-site.
Will it improve quality? We certainly hope so – it should do.
Will it lower costs? Again, yes it should, but whether that manifests itself as lower prices for home owners, that’s yet to be seen.
Will it change everything in the building scene? Probably not – it’s just one player, even if it is the biggest player in the market. But we’re going to be watching it with interest.
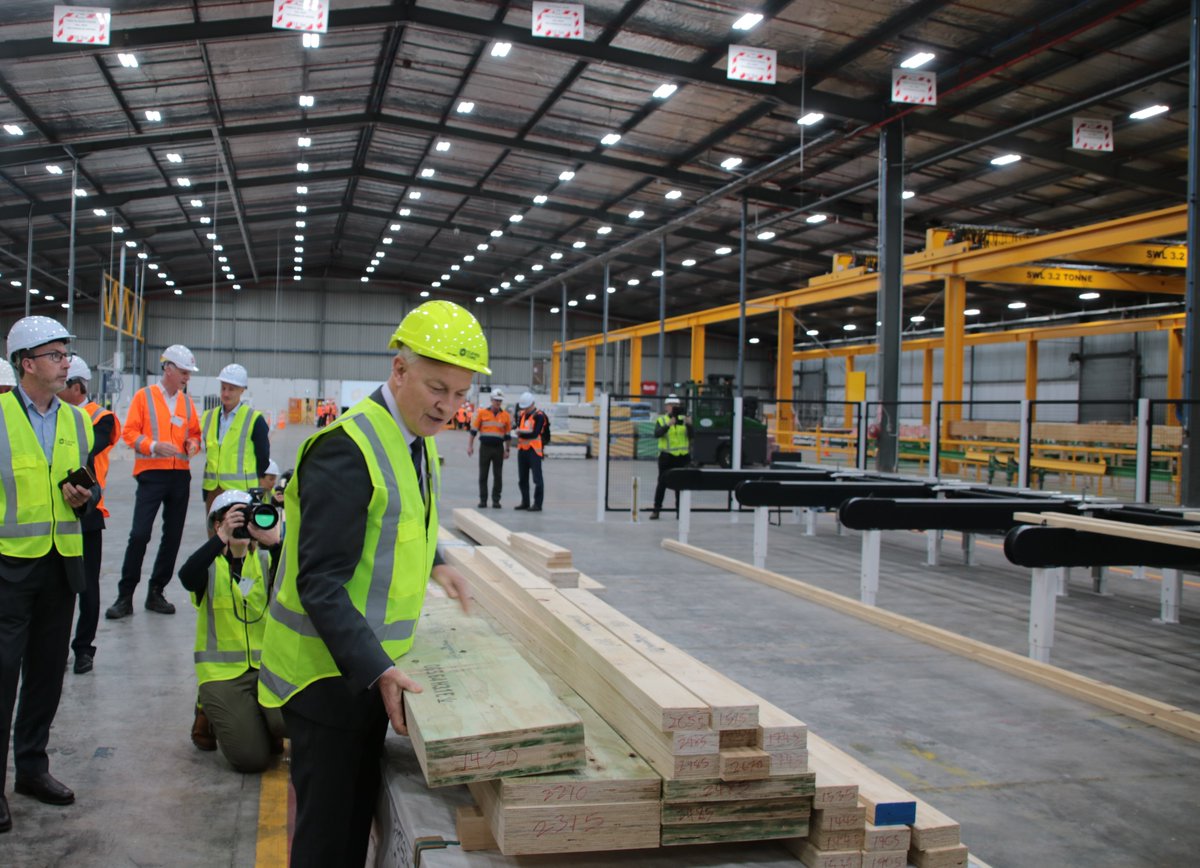
The Clever Core project is new for Fletchers but not new for New Zealand. Pam Bell’s book on Kiwi Prefab shows clearly that NZ has always had prefab buildings, with surges of output at various times through the years. The first treaty house at Waitangi was an Aussie import, flat-packed, and still going well now (although many repairs over the years I’m sure). Keith Hay Homes were / are prefabricated, as are Lockwood, and many others. Many of the first State houses were Prefab, some imported from Austria (particularly those at Titahi Bay apparently), while the Railway houses were all prefabbed and dropped off the side of a railway wagon in pieces as the iron road made its way through early NZ. There’s also the massive Concision factory in the South Island – but Fletcher’s project is even bigger than this.
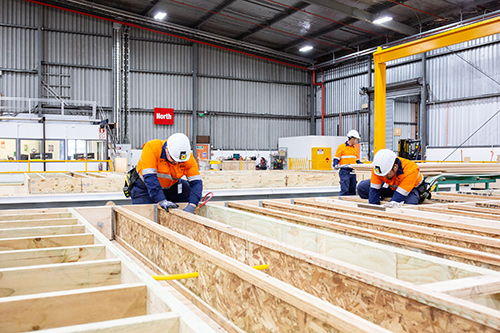
Apparently capable of pumping out 500 houses a year, the Clever Core will therefore be producing 1-2 houses per day. “Clever Core is New Zealand’s largest purpose-designed, off-site home manufacturing facility. Clever Core produces the core structural components of a home – wall, floor and roof panels - in a factory environment, in as little as a day. This core is then assembled on site over another 24 hours, and finished within only 6-10 weeks (compared for 22 weeks for a standard build).” So what it seems to do is to build panels rather than volumes – wall panels, floor panels, and if we can judge Fletcher’s experiments before, then maybe the entire roof goes on in one shot.
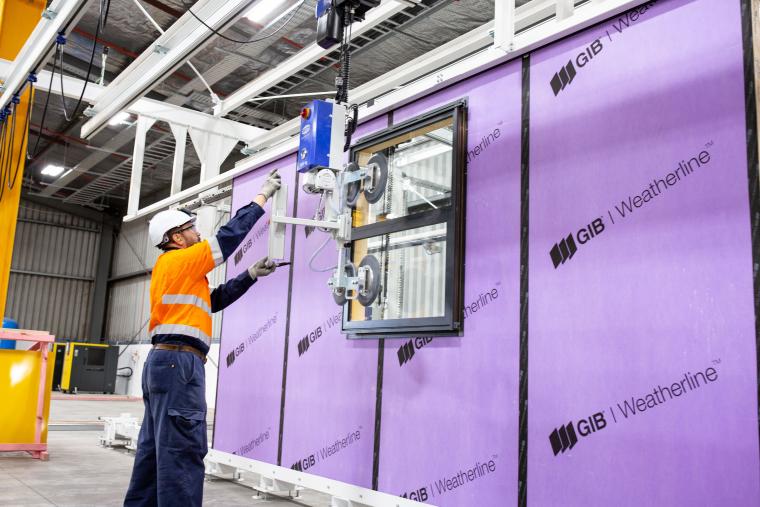
“Fletcher Living’s developments at Ormiston, Swanson and Beachlands are the first to receive Clever Core structural components, which will speed up delivery and allow people to move in before Christmas. These (100) houses will be indistinguishable in appearance from their traditionally built neighbours once the exterior claddings and facia are added and internal fit-outs are completed.” Following with interest!
“indistinguishable in appearance from their traditionally built neighbours”…
That’s a shame.
Aaah yes, well, you have a point there. I have no idea who Fletcher employs as Architects – if indeed they do employ any at all – but yes, they are pretty crap and boring for the most part. Much like the tastes of the average kiwi perhaps? We don’t have a high level of architectural cognisance amongst the population, to put it bluntly. But my hope is, that if we can get the machines to build our houses better than our Auckland cowboys can, then perhaps one day we can upgrade their software? Not in a Terminator, Skynet sort of upgrade, but perhaps just more an aesthetic upgrade….
I see the job of an architect as finding the sweet spot between what the client wants, and what the technology and materials can deliver. So, if it’s boring, blame the architect, not the manufacturing process. I admit in this case Fletcher may be playing both roles.
I recall the HoffHouse in Grand Designs UK. I never really understand how they handled plumbing, electric wiring, etc where the panels met. I guess minimizing the number of wet walls helps for the plumbing. For the wiring, having wireless light switches means that each panel only needs a single power-in connection (plus a power-out if you want to daisy-chain them). This does not, however, sit well with the current electrical wiring regulations without a secondary fuse box in each panel.
This is quite exciting – we’re about to join the twentieth century!
well spotted Kevin – the wiring does indeed have to be very well thought through and perfectly carried out in a HoffHaus, as their finishing standards are going to be set quite high. I know with some CLT panel manufacturers they will drill a long hole up into the panel, for the later insertion of a wire. Others just run all the wiring up through the floor and into the skirting for powerpoint etc. I’m not sure what Fletchers will do with their wires, but there are now modular wiring systems out and about that simplify matters greatly.